In April, LD Davis celebrated one year since implementing our Enterprise Resource Planning (ERP) system. What a year it has been!
We recently sat down with our Office Manager, Halee Ellis, who is based out of our North Carolina manufacturing facility. Halee played a major role in the implementation process of the ERP, so we want to check in with her to see how things are going a year later.
How has our new ERP system changed our Standard Operation Procedures?
Our ERP has changed our Standard Operating Procedures in every department for the better. Procedures have been streamlined everywhere from Order Entry, all of the way through to the shipping process. It has provided us better accessibility, cross training, communication, and real time view of supply and demand.
With the new system, information is much more readily retrievable. Generally, our team will find reports/functions within the system that display the information they require most frequently. They then save shortcuts to their desk tops for quick and easy access.
The new system has also made it much easier to cross train our staff. This has been a great way to help everyone better understand the bigger picture of our operation at LD Davis. It has helped our organization socially, as we are now operating as a team that understands the value and function of every role.
Our ERP has made it much easier to communicate with customers and vendors alike. For our customers, we can store their contact information, order history, shipping locations, and preferences in one customer file location. Our vendor communications have been improved by the ability to send purchase orders directly from within our system, complete with notes and specifications, via email.
In our new system, demand is generated for every SKU in the formula of the item ordered in proportion to the amount of finished goods on order. The system does all of that for us at the time of order entry. The ability to see usage and demand for our glue products in real time has been a real game changer for us. This has been my #1 favorite improvement of process.
What would you do differently if you were to implement the ERP over again?
If we were to implement ERP over again, I would get more sleep and do more yoga. When you’re stuck in a conference room with the same individuals for months on end, you should really take time to properly decompress. We joke that I got my first wrinkle during this process - haha!
Methodically, I honestly wouldn’t change a thing. I learned things in the four months of being hunkered down in that room that had so much and so little to do with a computer system. I learned so much about our company, business, human nature, and myself that I wouldn’t take anything back. Sure, I learned a lot about ERP technically; but what I value most about the experience is what ERP taught me about life: listen first, question everything, and “that’s how we’ve always done it” is never a valid answer for moving forward.
What aspects of implementation were easier than you expected?
Lunch. We ate a lot of pizza and fast food during this time. Otherwise, almost everything seemed to have a catch to it, something we previously overlooked, or didn’t have a clear understanding of initially… but we put our best foot forward, and figured it out one day at a time.
I do, however, think that the process was much simpler once were able to wrap our minds around the way the system “thinks”. We had to put our own thought processes and opinions aside, and think like the system as it is written.
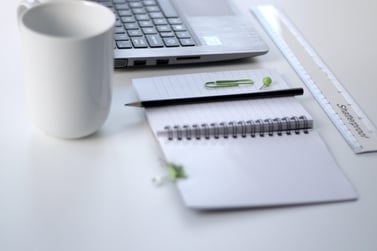
For example: A child can be told, “go brush your teeth,” and they can perform the task completely. An ERP system needs to be told, “stand up, walk to the bathroom, turn on the light, pick up toothbrush, turn on water, wet tooth brush…” . Once we understood that concept, it was much easier to move forward. I’m thankful this light bulb switched on fairly early for us.
What aspects of implementation were harder than you expected?
Uploading BOM’s (Bill of Materials), Standard Costs for Raw Materials, and getting the UOM’s correct. They were the tedious “little things” that just when we thought we were done, we’d find another one. It was incredibly humbling, but we came out far more knowledgeable for it with every little (& big) “uh-oh”, keystroke, phone call, and email it took us to make it right.
Do you feel that having an ERP system has made us a better vendor for our customers? How so?
Absolutely.
Our ability to service our customers has greatly improved with the increased transparency the system has given us. We can save any customer specific information necessary to their file, which is visible with every order from the point of order entry, all the way through to shipping. This makes it much easier to give our customers consistent results and excellent customer service.
Advice for those looking/planning to implement a new ERP system:
Preparation is everything. Seriously consider choosing a company that offers onsite implementation training and customization. This was a huge help to our team. Our Implementation Specialist kept us grounded when we had delusions of grandeur, encouraged us when we hit walls, and was an invaluable wealth of knowledge. It was great for us to have someone in-house that was intimately familiar with the base programming and add-ons/customization programming our company had chosen.
Our specialist constantly reminded us of this phrase: “Garbage in, garbage out”. You must invest in the programming and implementation with serious time, effort, and thought. Remember that you, and everyone else using the system, will reap what you sew on a daily basis.
Overall, I am very happy with the capabilities our new ERP has given us. I am thankful to have been a part of such a game changing move within our company. I feel a deep sense of pride for all of those who were a part of this process. Their resilience and positive outlook was inspiring.