Corrugated boxes are the lifeblood of the modern packaging and shipping industries. Think about it; almost everything we touch has been packaged, moved, delivered, and received in a brown box.
Packaging plays an important part in our everyday lives. To improve how we move things from point A to B it’s necessary to learn all the ins and outs of how manufacturers go about making corrugated boxes.
The Basics of Corrugated Cardboard and Terminology
When you mention cardboard, people tend to think of those big, brown boxes used for shipping items. If you’re not in the packaging industry, you probably don’t know that cardboard usually refers to a think paper stock or heavy paper-pulp. Cardboard is actually the heavy paper used to create cereal boxes, tissues, greeting cards, and more. Although corrugated boxes are made with cardboard, it’s not exactly the same.
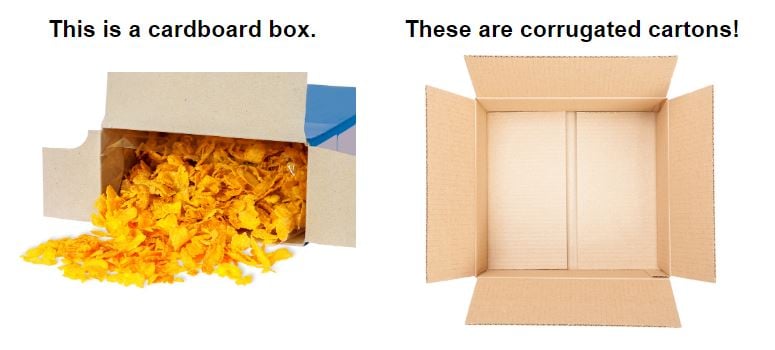
Corrugated is made from three layers of thick paper stock that are glued together. Two flat outside pieces called liners have a layer of grooved cardboard sandwiched between them. The wavy piece of paper stock is called fluted cardboard, and it comes in different sizes to provide different levels of strength.
.jpg)
The Life Cycle of Corrugated Carton Packaging
Corrugated packaging is one of the most frequently used shipping materials. In fact, 95% of all products in the United States are shipped in corrugated boxes because they are cost-effective, lightweight, and recyclable. The boxes can handle the pressure that comes with stacking because of their layered design, making them ideal for easy transporting.
Businesses like to use corrugated boxes because of how reusable the material is. Corrugated cardboard is one of the greenest packaging solutions because it’s made with a higher percentage of recycled materials that can be reused again and again. But how does the process of making a corrugated box begin?
Step 1: Gathering the Materials
It’s pretty standard for corrugated cardboard to be made mostly from recycled content, often sourced from old cardboard and paper stock. Recycled cardboard only takes about 75% of the energy needed to make new cardboard. Each time cardboard is recycled the fibers weaken. This means that cardboard can only be recycled about eight times.
While most corrugated boxes are created from recycled paper, it is necessary to make new cardboard with virgin pulp from newly harvested trees. Fast growing, sustainable pine trees are the primary raw material used to make corrugated cardboard. Once the trees have been cut, they are stripped of their limbs, and the trunks are shipped to a pulp mill.
Step 2. The Pulping Process
At the mill, the wood is turned into paper using the kraft process. First, tree trunks are turned into wood chips before the wood is treated with chemicals to break it down into a fibrous pulp. After pulping and processing, the fibers are sent to the paper machine and are formed, pressed, fired, and rolled into big, heavy rolls of brown craft paper.
Step 3. Manufacturing and Fluting
To create the wavy paper stock in the middle, the rolls of kraft paper are fed into a corrugated roller machine. Interestingly, corrugated rollers have been around since the 18th century, and were once used to add ruffles to clothes like shirts and hats. Once the paper is through the corrugator, glue is used to adhere the liners to both sides. Now that the corrugate is together, it is cut into the desired shape of the box and is ready to be packaged, bundled together, and sent for distribution.
Step 4. Usage
The main industries that use corrugated cartons are the food and shipping industries. Corrugated boxes are inexpensive to make and provide a stable cushion for products stored inside, keeping items safe during transportation. Not only is this type of packaging strong, lightweight, and cost-effective, it’s also food-safe. Corrugated boxes are often manufactured using eco-friendly glues, making them safe for food storage and better for the environment.
Step 5. Recycling
Once used, corrugated boxes are sorted into recycling and sent back to the paper mill. There the process begins all over again! The corrugated cardboard is soaked in water and chemicals to break it down and all coloring and stables are removed. The broken down corrugated is then mixed with virgin fibers and remade into new corrugated cartons!
Corrugated cardboard can be recycled up to 8 times, making it one of the most sustainable and cost-effective types of packaging to use. Using eco-friendly glues, like liquid or gelatin-based glues also make recycling corrugated far easier and better for the planet.
The Future of Sustainable Packaging
As we look ahead at the future of the packaging and shipping industries, it’s important to understand that a lot goes into making the perfect package. Sustainability is key as the local and global economies become more reliant transporting goods and products quickly and effectively.
If you’re looking for a way to improve the sustainability and environmental impact of your packaging, considering the adhesive that holds it all together could be a game-changer. To learn more about how using biodegradable glue can improve your packaging production, contact the experts at LD Davis.