Staying at the forefront of glue manufacturing requires innovation. When you’re one of the world’s oldest manufacturers and compounders of gelatin glue, your equipment may need an upgrade. Recently, Lee Process Equipment™ (LPE) helped our facility in Monroe, NC replace four existing fountain blenders to improve our bulk material handling process.
The way gelatin glue is manufactured and applied has changed over the decades. Our gelatin glue formulas are exceptionally environmentally friendly and are 100% non-toxic, recyclable, and biodegradable. These glues are commonly used in the manufacturing of rigid boxes, bookbinding, and laminating.
The experts at LPE worked with us to engineer a materials handling solution that fit our needs, enabling us to serve our customers better now and in the future.
The Challenge
Applications for gelatin glue have expanded into a variety of industries. If you have ever purchased a board game, a puzzle, fine jewelry, perfume, or chocolates, you have likely brought home a high-quality rigid box created with LD Davis gelatin glue. To meet the growing demand for eco-friendly adhesives, we had to rethink our processing methods.
Ultimately, we discovered that our facility needed a higher capacity system that was faster, easier to operate, and more efficient than our previous equipment. The team at LPE, led by Mathias Lee, has a long working relationship with LD Davis Plant Manager Patrick Bryant. LPE’s industry expertise helped us design and implement a new bulk material handling system.
Adhesive Handling Requirements
We met with LPE and disused the following requirements our material system needs:
- Empty bulk bags of technical gelatin granules with various viscosities.
- Convey the gelatin granules to a screener.
- Screen the gelatin granules to filter out impurities and lumps.
- Blend a significantly higher volume of raw materials with different viscosities to meet specific lab requirements without product degradation, clumping, or material bridging.
- Fill bulk bags and smaller 50 lb. bags per customer needs.
- Maximize safety with a hazard analysis and risk mitigation study for a system designed to the highest safety levels, including SIL 4 safety measures.
- Minimize operator time and be a ‘one-person operation.’
- Minimize process time through every step, including raw material bulk bag unloading, conveying time, screening time, mixer loading time, mixing time, bulk bag filling, and 50 lb. bag packing time.
- Minimize the factory floor footprint.
- Improve equipment accessibility and layout.
Solution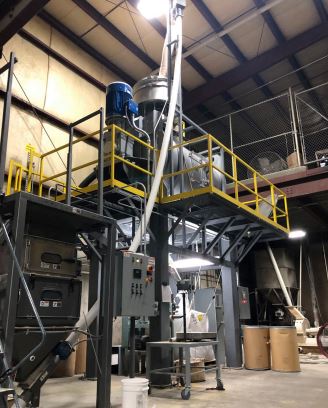
We worked closely with the experts at LPE, who were chosen to design and install our new bulk material handling system. The result is a state-of-the-art, reliable bulk material handling solution that resolves all previous challenges and increases production capacity by 60%.
- LPE recommended the installation company that was contracted to manufacture a steel structure with a mezzanine to secure all equipment for maximum stability and safety.
- Bulk bags of selected raw materials are emptied with a Spiroflow T2 bulk bag discharger.
- The materials are conveyed from the bulk bag discharger to a screener via a Spiroflow FSC412-B flexible screw conveyor fitted with a flat spiral which can convey up to 275 cubic feet of material per hour.
- Raw materials are fed through a screener that is located above a MIXSYS Ploughshare mixer. Large particles and foreign materials caught by the screen are discharged to a 55-gallon drum.
- Screened materials are then mixed by the MIXSYS Ploughshare 3D mixer fitted with three chopper motors. The mixer is designed with air purged bearings and a specialty discharge design. This massive mixer can mix up to 3 bulk bags of material at a time. MIXSYS Ploughshare Mixers are the most efficient mixers globally and consist of a horizontal cylindrical container with multiple plow-shaped shovels mounted on the main shaft. The mixer volume can vary by 15 - 85%, allowing for various batch sizes and increased flexibility in only one machine.
- The mixed material is then released into an existing bulk bag filler fitted with a floor scale or an existing 55-lb sack packer.
- The filled bags are removed and shipped to the customer.
- All equipment is operated via a custom programmed Spiroflow Automation Solutions control system utilizing various safety relays for simple, safe, and reliable operation.
- Various Lorenz clamps were included in the design.
- Lee Process Equipment supplied flexible connections where required.
Results
The new bulk material handling system met and exceeded expectations. Bryant stated, “LPE and their associate vendors could not have made this project any more accessible. We have a system design that will last well into the future, creating the best product possible for our customers. We look forward to future projects with LPE.”
Improvements to our bulk material handling system include:
- Operator safety was significantly increased with Spiroflow’s comprehensive control systems fitted with safety relays to operate each new piece of capital equipment.
- Operator labor was reduced by 40%.
- Mixing capacity increased from 3,000 lb. to 4,000 lb. (33% improvement).
- The time to fill the mixer was reduced from 30-40 minutes to 10-15 minutes (64% improvement).
- Mixing time was exponentially reduced, thereby exceeding LD Davis’ expectations.
- Material bridging is no longer an issue.
- Ergonomic Footprint: The original configuration was spread out over two levels and required 640 sq ft of factory floor space. The new system occupies a compact area requiring only 240 sq ft (62.5% reduction). Access to the top of the flexible screw conveyor, screener, and mixer is provided via the steel mezzanine.
About Lee Process Equipment
Lee Process Equipment is a full-service representative and consulting agency. Covering the entire states of North Carolina, South Carolina, and Virginia, Lee Process Equipment has been involved in successful projects for the food, chemical, recycling, plastics markets. From simple components to complex processing lines, Lee Process is the leader in supplying applications for conveying, packaging, storing, batching, blending, and emptying products in various industries.
The Future of Gelatin Material Handling
Now more than ever, LD Davis is capable of helping manufacturers in the United States get the eco-friendly adhesives needed. Improve your sustainability practices with gelatin-based glue.